各种炭素原料经过混捏成形后,虽然在外形上具有一定的尺寸和形状,但它只是通过黏结剂的物理黏结作用形成的整体,黏合剂未炭化(或称焦化),在机械强度上与理化性能上还远远达不到炭素材料的使用性能。所以在炭素生产工艺过程中还必须经过加热处理的过程,这种将生胚在加热炉内的保护介质中,在隔绝空气条件下,按一定升温速度进行加热处理的过程就称为焙烧。对于电极糊产品,其焙烧过程在矿热电炉中完成,又称自焙电极,其反应机理与预焙电极基本相似,这里主要介绍下理想状况的焙烧工艺。
焙烧过程实际上是使生胚通过热处理(大约1000℃)将黏结剂炭化为黏结剂焦的过程。即将压制好的生胚放置在焙烧炉内,隔绝空气进行加热,黏结剂在一定温度下,进行一系列的物理化学反应,总称为焦化反应或炭化反应,在炭骨料表面生成一定厚度的黏结剂胶膜,通过黏结剂焦而使炭粉颗粒与颗粒之间连接成具有一定机械强度和理化性能的整体。焙烧过程是一个初期炭化过程。但它形成了对高温炭质的性质有决定意义的基本结构,是炭化中最重要的过程,特别是液相炭化过程,如果控制了炭化反应,就能制得高强度的黏结剂焦。经过焙烧阶段,生胚发生显著变化,体积收缩,强度提高,但由于微孔的形成,体积密度稍有降低,而热导率和电导率大为提高。
①获得黏结焦,使分散的炭颗粒能成为有机的整体,也就是使黏结剂完成炭化过程;②使制品结构趋于更加均匀,且无内外裂纹、空洞与气孔等缺陷;③使制品具有一定的几何尺寸、形状和机械强度及性能。焙烧制品的机械强度和性能取决于焙烧时黏结剂转变成黏结剂焦炭的数量,而机械性能与焦化值有直接关系。毛坯在焙烧过程中的焦化反应过程受到各种条件如升温速度、体系的气氛和压力、装炉方法、填充料等的影响而变得极为复杂,就焙烧过程而言,黏结剂分解、缩聚、成焦并不是均匀进行,而是呈现一定阶段性,大致上可把焙烧过程分为四个阶段。
第一阶段为预热阶段,室温至明火温度约350℃,制品温度在200℃左右,在此阶段中主要是黏结剂软化。制品在此阶段中处于塑性状态,体积略有膨胀,这时,由于制品体内的温差和压力差,黏结剂产生迁移,液态的黏结剂缓慢地扩散、流动、重新分布,但还没有发生明显的化学和物理化学变化,主要排出吸附水。第二阶段为成焦阶段,明火温度350-800℃,制品温度200〜700℃,制品温度在300℃以下时,毛坯随着温度升高而排出水分、二氧化碳、轻油等,并部分进行脱氢缩聚反应,主要是沥青中的石油质和沥青质逐渐缩聚成分子量更大的苯不溶物,由于热分解而新形成的物质的排出几乎占挥发物总量的20%。300℃以上时,此阶段是影响焙烧质量的关键阶段。黏结剂进行大量复杂的分解、聚合、环化、芳构化反应,黏结剂进行分解并和分解产物的再聚合同时进行,形成中间相、中间相长大,形成前驱体。在400℃时,制品开始出现结焦,但强度仍很低,而沥青的黏结性降低。500℃左右,虽然还有少量挥发分,但炭的基本结构己形成。500〜550℃形成半焦,由沥青热分解而生成的挥发物,基本上在600〜650℃以前排出,700〜750℃形成焦炭。为了提高沥青析焦率,改善制品理化性能,该阶段必须均匀缓慢地升温。若升温过快,挥发分急剧排除,制品内外温差加大,引起热应力,就会导致制品裂纹的生成。此外,在这阶段排出的大量挥发分充满着整个炉室,这些气体在炽热的制品表面分解,而产生固体碳,沉积在制品的气孔和表面上,提高了产焦率,并使制品的孔隙封闭,强度提高。本阶段反应最主要的特点是,官能团的聚合和分解及排出的气体中氢含量逐渐增加。第三阶段为排除外围异类原子阶段,明火温度800〜1100℃,制品温度700-1000℃之间。在此阶段中,黏结焦中形成大型的芳香族平面分子,平面分子的外围异类原子及原子基团发生断裂被排除,随着温度的升高,平面分子发生重排现象。900℃以上边缘氢原子逐渐断裂与排除,同时黏结剂焦进一步收缩及致密化,这时,化学过程逐渐减弱,内外收缩逐渐减少,而真密度、强度、导电性都增加。在高温烧结阶段,升温速率可以提高一些,在达到最高温度后,还要保温15〜20h。第四阶段为冷却阶段,冷却时,降温速率可以比升温速率稍快些,但由于制品热导率的限制,制品内部降温速率小于表面的降温速率,从而从制品中心到表面形成大小不同的温度梯度及热应力梯度。若热应力过大,会引起内外收缩不均匀而产生裂纹,所以降温也要有控制地进行。焙烧过程中,黏结剂的迁移是使焙烧制品产生轴向和径向不均匀的一个主要因素。黏结剂迁移有下列规律:
①黏结剂的迁移有两个阶段,第一阶段在混捏过程中发生,第二阶段在焙烧过程中发生;②在120℃左右,黏结剂就开始迁移,之后,黏结剂的迁移速度急剧增加,在180〜200℃时达到最大值,温度高于230℃,黏结剂的迁移过程就停止了;③黏结剂迁移过程中,有选择性迁移现象,即黏结剂中的轻质组分更易于迁移:④黏结剂迁移与重力有关系,液态黏结剂都是从上端向下端迁移;⑤在相同温度条件下,骨料的粒度组成愈粗,黏结剂就愈容易迁移;⑥加热时,升温速度愈慢,迁移程度愈大,这就更说明焙烧过程的低温阶段,升温速度应该快,以减少黏结剂的迁移。焙烧的主要目的是使黏结剂成为黏结焦,把骨料颗粒连接成一个整体。黏结剂焦化的实质是炭化反应。一般炭素制品都用煤沥青作为黏结剂,煤沥青的成焦过程即是煤沥青进行分解、环化、芳构化和缩聚等反应的综合过程。煤沥青的炭化是液相炭化,在350〜400℃之间形成中间相小球体,这种小球体随加热温度升高进行融并、长大,最终生成可石墨化炭。但黏结剂的炭化过程与单纯沥青的炭化过程有着-定的差异,这一方面是因为黏结剂沥青中含有10%〜20%的游离碳,它会妨碍中间相小球体的融并和长大,另一方面,更为突出的是因为黏结剂沥青填满骨料的间隙,以薄膜形态受到热处理,从而使它的炭化有以下特点。①黏结剂是在与骨料表面接触的情况下进行炭化,所以不能忽视骨料表面活性的影响。实际上,黏结剂沥青在焙烧过程中的炭化具有氧化脱氢的特征。骨料表面在与黏结剂混合前已不同程度地吸附了O2、CO和CO2等,在加热到300℃时,就对黏结剂中各组分进行有选择的化学吸附,这些骨料具有与黏结剂分子或官能团进行氧化还原反应的活性。经测试得知,石油焦和中温沥青混合物在270-300℃的范围内有很强的放热峰,而单纯沥青在此温度范围内的峰很弱,证明在这一温度区间内,骨料表面与黏结剂之间有放热反应的化学结合。②骨料表面吸附的氧和碳的氧化物将促进黏结剂分子的脱氢缩聚作用,也将促使骨料表面和黏结剂交叉键的形成和沥青提前固化。这种反应将妨碍中间相小球体的生成,从而降低黏结剂焦的可石墨化程度。黏结剤氧化脱氢缩聚反应的结果是使析焦量增加,焙烧晶的密度和强度提高。③黏结剂与骨料接触面呈薄膜状,所以反应面积大,反应(热分解和热缩聚)速度快,影响屮间相小球体的融并与长大。④黏结剂填满骨料间隙,流动性受限制,逸出气体(气泡)引起液相搅拌不均匀。(1)生制品的体积变化在焙烧过程中,生制品的外表尺寸一直在变化,总的来说,它的体积是收缩的,但有时尺寸也可能出现增大。生制品体积的不均匀收缩会导致内外缺陷的产生,直到形成裂纹。收缩与压型时的压实程度、压制方法,黏结剂质量和用量,骨材的锻烧程度、锻烧温度和加热速度等有关。这些因素通常是交织在一起的。
收缩是随着焙烧温度的升高而逐渐产生的。冷压成型制品出现收缩的温度低,热压成型和气孔率低的生制品在开始加热时不产生收缩,在100℃时体积开始增加,到400℃达到最大值,从400℃开始收缩速度急剧增加,直到800℃之后,收缩速度下降。生制品收缩与压型时压实程度的关系列于表1。生制品的体积密度愈低、压型时单位压力愈小,则收缩愈大。
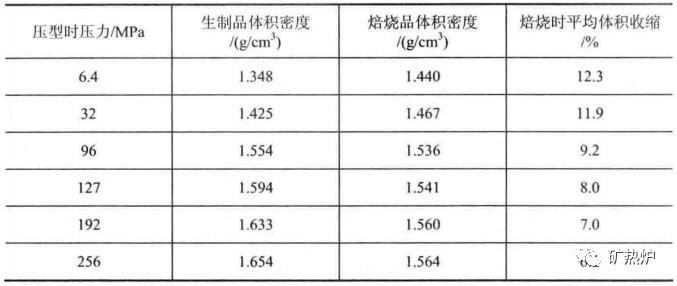
生制品收缩与黏结剂含量呈线性关系。生制品中含黏结剂量过大时,收缩加大,易于产生变形并出现裂纹。黏结剂的性质对收缩也有影响,轻质黏结剂的挥发分排出量大,对收缩的影响大。沥青中不溶物质含量增加,收缩减少。收缩与粒度组成也有一定的关系,混合料的粒度组成愈细,收缩就愈大。制品收缩在很大程度上与焙烧条件有关,如装入生制品的炉室尺寸和生制品在炉室中的分布位置,填充料的物理性质和粒度组成,燃气介质等。这些都是各种焙烧晶和同一根制品不同部位产生不均匀收缩的重要原因。(1)生制品物理化学性质在焙烧过程中的变化在焙烧过程中生制品物理化学性质的变化如表2所示。焙烧制品与生制品相比较,真密度由1.76g/cm³提高到1.99g/cm3,体积密度由1.68g/cm³下降到1.50g/cm³,电阻率由1.66×10⁻²Ω・m下降到5.5×10⁻⁵Ω·m,气孔率由3.06%上升为23.79%,质量损失为10.78%。
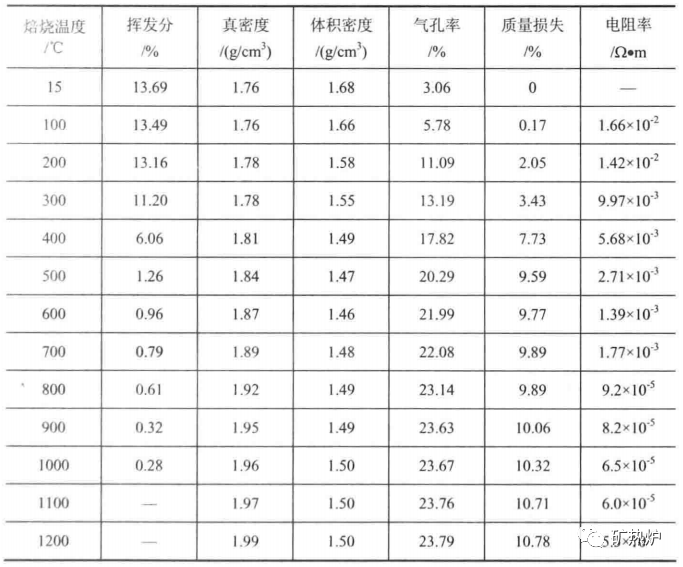
焙烧制品的质量不仅与配料、混捏、压型等工序有关,而且受到焙烧工序的炉内气氛、压力、升温速度、最终温度、填充料性质以及装炉方法等多种工艺因素的影响。
(1)焙烧体系中气氛的影响焙烧时,生制品装在焙烧箱内,周围覆盖着填充料,热是通过填料层到达生制品。这一个空间就构成一个焙烧体系。如果焙烧是在倒焰窑中进行,则整个窑室是一个焙烧体系,如果焙烧是在环式炉中进行,由于热气流顺序通过各个炉室,所以各炉室连成一个焙烧体系。在焙烧过程中,由于生制品中黏结剂的热分解和热缩聚反应,在生制品内部及周围形成一定的焙烧气氛。如果焙烧体系是一个封闭体系,则黏结剂热分解产生的气体从生制品中逸出,扩散到整个炉室,使分压逐渐增大,直到一个极限,即黏结剂的饱和蒸气压。这时,在生制品表面逸出的分子数与凝结的分子数达到平衡。但实际的焙烧过程并不在封闭体系中进行,黏结剂分解生成的气体不断地通过制品内部和填充剂间隙,随热气流进入烟道而排岀,致使制品内外层和填充料内外层之间都存在着分解气体的浓度梯度,使气体不断向外扩散。若填充料和炉室上部空间的分解气体浓度低,则分解气体从制品中向外扩散的速度快,促进了黏结剂热分解反应的进行,使黏结剂的析焦量相应减少。反之,若分解气体排出速度慢,则析焦量就增加。其次,在焙烧体系中存在着氧,氧除了来源于混捏前干骨料和填充料吸附的氧以外,主要是从燃料气中来。一般热气流中含氧量占10%〜16%,此外,还有从炉墙泄漏处侵入的空气。黏结剂焦化具有氧化脱氢缩聚反应,黏结剂氧化,有利于析焦量的增加。但受氧侵入的生制品表层收缩率降低,造成内外收缩不一致,就会产生硬壳型废品,这种制品的表层和内层之间出现裂纹,这种废品往往在靠近炉室壁和砖槽壁一侧出现较多,这是因为靠近炉室壁处氧的浓度最高。为了减少硬壳型废品率,就需要采取使制品与氧隔绝的措施,如及时修补炉墙,保证填充料的覆盖厚度等。(2)压力的影响当焙烧体系达到300〜400℃时,黏结剂的分解和缩聚反应同时进行,如果此时增加体系的压力,反应将向缩聚方向移动。同时,提高焙烧压力还可减少分解产物的浓度梯度,使第一次反应产物在焙烧体系中延长停留时间,有利于参与缩聚反应,既可以提高析焦量,又有利于中间相小球体的生成。在焙烧前期,当黏结剂还处于低黏度的熔融状态时,增加体系压力,可使黏结剂渗入骨料内部的微孔及微裂纹中,增强了骨料颗粒间的结合,使制品进一步致密化。由于在一定压力下焦化,液体的表面张力使新生成的气孔内壁呈平滑的圆形,避免了在常压焙烧时生成的多角形气孔而产生应力集中的现象。因此,在相同体积密度的情况下,加压焙烧制品的机械强度高,抗压强度比常压焙烧的制品增加30%,抗折强度提高40%左右。在压力下焙烧,可以消除生制品的应力弛放过程,同时加压焙烧必然是一个密闭系统,可以防止生制品氧化。在加热过程中,制品内外收缩均匀,避免造成硬壳型裂纹。由于收缩均匀,就可以适当提高升温速度,缩短焙烧时间。如100mm的制品常压下焙烧需150〜200h,而釆用高压焙烧仅需50h,提高了生产效率。因此,加压焙烧是一项有前途的焙烧新技术。(3)加热速率的影响升温速率对黏结剂的析焦量及制品的密度有很大影响(表3)。升温速率较慢时,黏结剂有足够时间进行分解及缩聚,所以析焦量增加,制品的密度增大,物理机械性能也有所提髙。同时,升温速率较慢,可以形成焙烧体系内必要的均匀温度场,使制品内外温差小,防止制品裂纹的生成。反之,升温速率过快,在同一个制品中就同时进行着不同阶段的焦化反应,引起生制品内外收缩不均匀,而产生内应力。这种内应力在300℃以内将使制品变形,在500℃以上,制品外层黏结剂已固化,内应力将使制品开裂。
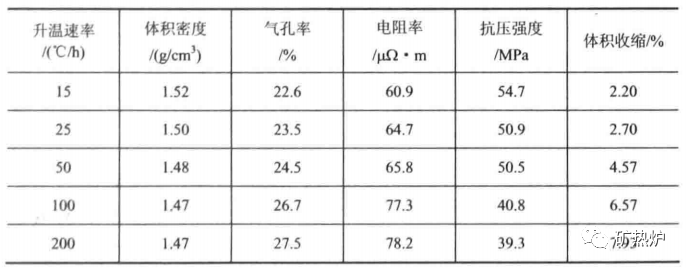
但在400℃以前的升温速率不宜过慢,否则就延长了黏结剂焦化的时间,将使带硬壳型裂纹的废品增加。冷却速率一般比升温速率快,但也不能太快,否则制品内外温度梯度过大,也会造成制品开裂。一般将降温速率控制在50C/h以下,到800℃以下则可任其自然冷却。