大家都知道,钢包渣线是钢水与空气直接接触的部位该部位由于温差与富氧环境的存在,使得侵蚀速度较其他部位明显加快,再加上钢水在运转过程中的倾翻及排渣作业,对渣线造成很大程度的破坏,因此钢包渣线的侵蚀一直以来都是炼钢炼铁行业的一个瓶颈问题,渣线位置不仅会出现侵蚀过快,还有结渣、发红、剥落、漏钢等等问题。渣线砖一般是指钢包口向下数第三层至第八层区域内砌筑的耐火砖。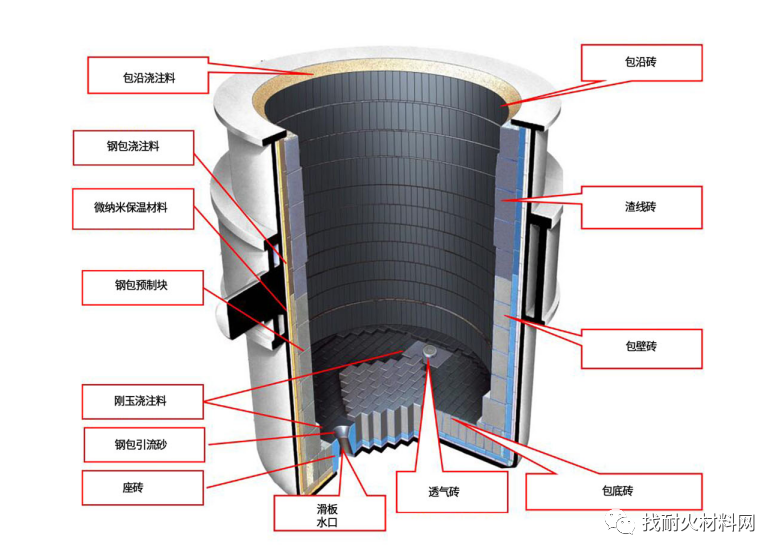
目前炼钢生产中,较为广泛的是在渣线位置使用镁碳质的耐火材料,从之前的镁碳砖砌筑到后来镁碳质浇注料的整体浇注,综合精炼过程当中的内衬问题的话,影响这个环节整体炉衬寿命的、损毁情况最严重的还是渣线部位。那么今天我们从多个案例分析当中,针对渣线部位的损毁及耐材分析和冶炼工况环境及冶炼原料这几个方面来对这个问题进行探讨。钢包精炼炉常见的设备包括LF炉、VD炉、VOD炉、RH炉、AHF炉等,常见的钢包渣线部位耐材问题是渣线侵蚀过快,耐火内衬发红、出现孔洞、渣沟或者是渣线部位出现深凹坑等现象,尤以LF炉的渣线部位侵蚀最为常见和严重。1) LF 精炼温度 1550~1610 ℃,精炼时间:35-45min;2)VD炉真空脱气,处理温度1550~1610℃,时间大于20min;3)精炼时造白渣,使用精炼合成渣、埋弧渣,碱度高(CaO与SiO2的质量比大于3.5);5)出钢温度平均在1650℃以上,钢水在钢包停留时间平均在130min 以上。随着钢包二次精炼技术的发展,钢包用耐火材料也在这个过程中不断的朝前发展,它必须具备的条件有耐高温、耐热冲击、耐熔渣的侵蚀,还需要具有较高的机械强度、需要随钢水不断的搅动和冲刷。对于渣线部位侵蚀的主要原因归结为四大方面:一是工艺因素,这个就包括了在钢铁冶炼过程当中的搅拌强度、送电量、处理时间等等;二是精炼渣的成分问题,渣中的F、MgO、Al2O3、CaO、TFe等元素对渣线砖的影响;第三是耐火材料及砌筑质量;第四则是机械损伤。在这几个因素里面,精炼渣对镁碳砖的损毁是最大的,不同的冶炼钢品种以及里面所含的杂质不同,对于渣线砖的损毁程度也是不一样的,它的侵蚀过程一般为:氧化→脱碳→疏松→冲刷→脱落→损毁。钢包渣线砖的氧化主要是碳的氧化,包括气相氧化、液相氧化、间接氧化和气孔的影响。气相氧化是指碳的直接氧化,石墨在高温下与空气(O2)、水蒸汽(H2O)和碳酸气等共存而产生的氧化。液相氧化则是指熔渣中的铁和锰的氧化物引起碳的氧化,通常在冶炼过程中随着熔渣中总铁含量的增加,镁碳质的炉衬砖损毁速度就加剧。在这个过程当中,随着含碳制品表面形成脱碳层后,熔渣容易渗透并产生反应,导致衬砖的结构疏松,加快制品的损毁。间接氧化是在高温状态下MgO与碳产生反应,形成脱碳层,导致镁碳砖组织结构的恶化,这个过程中的损毁是最为严重的,熔渣向脱碳层不断的侵蚀,与镁砂形成反应层出现低熔物,最终引起镁碳砖的熔蚀和冲蚀。钢包渣线结渣则是指在钢水浇完之后仍有一部分挂留在钢包渣线位置,形成这个的原因主要有:一是钢水待浇时间长,冷却结壳在渣线部位结渣。二是钢渣中铝含量较高时,钢水粘稠度大,在钢水镇静过程中随着渣面温度降低而凝固在钢包的渣线部位。第三个因素是钢包渣线砖本身就有侵蚀,产生了凹坑或者凹陷(在下渣的过程中,随着钢渣中碱度的变化,钢包包壁与渣接触的衬砖逐渐被溶解、脱落而形成的凹陷)。当熔渣中碱度稳定后,熔渣与渣线砖互溶并结合形成新的结渣层,结渣越来越多并且越来越容易挂渣。如何改善渣线部位的损毁呢?这也是众多学者以及炼钢工作人员一直在研究的问题。我们针对多个钢厂的案例及实验室的验证提出以下几点,供参考:1.优化精炼系统、改善冶炼条件。精炼过程中往往会加入轻烧白云石,提高渣中氧化镁的浓度,以此来提高熔渣的碱度和黏度,降低渣中FeO的含量,经多个厂家实验,渣中FeO含量控制在0.5%左右、MgO含量控制在12%左右时,调整好炉渣的黏度,可有效降低炉渣对镁碳砖的侵蚀。2.采用更好的耐火材料。因为镁碳砖的抗侵蚀能力、抗热震性能主要受耐火砖原料的影响比较大,比如镁砂的质量,颗粒的分布以及添加剂的选用等因素。镁碳砖中使用的镁砂纯度越高,杂质中的B2O3越少,碳硫比例高,这时候衬砖的耐侵蚀效果越好。碳含量控制在14%左右的以电熔镁砂为原料的镁碳砖渣线抗侵蚀性越好。3.改变砌筑工艺、优化砖型设计。不管是新砌钢包还是小修的钢包,一定要注意耐火内衬的结构问题,比如平砌和立砌的差别,小修时新渣线与结合处的错台问题、砌筑时工作层与永久层之间胶泥的处理等等。4.控制吹氩、通电制度。LF炉一般会有三相电极,电极若位置进行偏移,则电极附近钢渣的热量及炉渣温度过高,会对渣线镁碳砖造成破坏性的侵蚀。6.在钢包内衬增加防氧化涂层。有些单位的钢包砌筑完毕进行烘烤时,并没有对烘烤过程中含碳工作层进行防氧化处理,导致烘烤结束后,镁碳砖层就已经有几十mm的氧化脱碳层。因此可以通过增加防氧化涂层来提高渣线部位镁碳砖的使用寿命。